“I prefer to attend this meeting when I am half asleep….then go eat my breakfast to get ready for the shift”
– overheard by a production line employee at a Fortune 50 company on attending the daily “all employee shift start” meeting.
Although these meetings may go by different names, we all know about the all-employee meeting that happens at the start of every manufacturing shift. Typically, the Shift Leader assembles all the production employees for the shift, reviews and assigns the tasks for the day, makes adjustments to the day’s schedule, discusses any key activities that require additional attention, and the team is off to start production. Seasoned manufacturing personnel know how important these meetings are to the performance of the employees and the overall plant in general.
Most manufacturing facilities that run on lean manufacturing principles have metrics to measure the plant’s safety, quality, cost, delivery, and personnel performance. Updating these metrics per shift, daily, weekly, or monthly varies with the practices and discipline enforced by the plant leadership. In a big plant, with a large number of lines, compiling these metrics and providing an overall summary of the production could become very meaningful. It helps the line personnel, who only see their own line, see the big picture and tie their performance to the overall performance of the plant.
Shift Production metrics are how shift and plant leadership could use some creativity to design a meaningful template to help the shift managers be proactive during the shift to make necessary changes in real time rather than waiting for the following day to see the results.
Referring back to the 5:40 am comments from one of the shop floor employees: mundane numbers and/or metrics data that they cannot do anything about are likely to elicit that response. To the employee’s point, when I attended the same 10-minute meeting, the shift leader discussed a (check-the-box) safety moment, project status, and some company announcements that had already been shared. The team then dispersed for a 20-minute breakfast break before start of production—hence the employee’s comment about breakfast.
Mundane first meetings are a missed opportunity for the line and plant leadership. These meetings can be the difference between high- and low-performing plants. In practice, this means measurable differences in safety, quality, productivity, and (customer) delivery of the plant. Successfully run production start-meetings are critical to success—or instrumental in the failure—of a plant.
There is a key set of criteria in successfully running these meetings and in keeping them engaging for the shop floor employees. But why doesn’t every plant follow these best practices? The answer: It often comes down to plant leadership, data availability, visibility of shift performance, company culture, and prioritizing what to measure (and share).
1. Plant Leadership:
It starts with accountability and the ownership of the leaders running production. Planning which metrics are important for each line, the frequency to post data, and what actions need to be taken from the data—needs to be planned by the leadership.
Managers from the best performing plants often tell us that they spend a lot of time planning these data extractions, and then how to use them during various meetings of the day. The level-1 meeting, also referred to as the start meeting, is focused on getting production started, while level-2 and level-3 meetings later in the shift / day / week are planned to make quick decisions and clear any obstacles holding out production.
The best performing plants develop actionable metrics with whatever data is readily available or collected live so that leaders can make decisions during the shift and not have to wait until end of shift to find out the performance of the line. Having leadership focus on right metrics, review them daily during shift runs, and actively involved in corrections could mean 15-20% improvement in plant productivity.
Figure: Impact of Various Drivers on Performance Improvement At a Plant
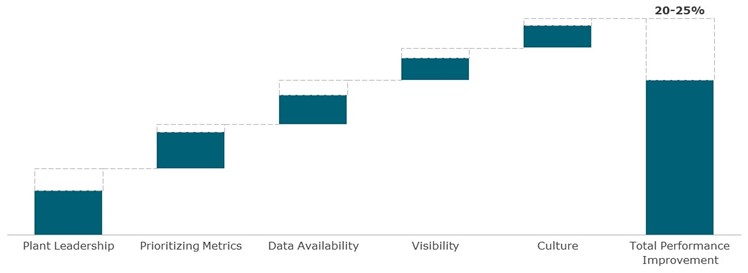
2. Data Availability:
Having a good Manufacturing Execution System (MES) and right level of automation where workstations are connected to the MES goes a long way in having readily accessible production data. Even in some of the better performing plants, a lack of readily available data is cited as a reason for reactive (vs proactive) assessment of production lines. Production leaders have to wait until the following day for someone to process the numbers and create outputs. While this is helpful to be aware of pitfalls if the same products are made, it is not useful if different products are made on that line, or if it is too late to make corrections during the production run. Planning to capture the right data that is actionable for both production and support personnel is a crucial best practice from top performing plants. This might include, for example, the number of lines down vs. how long the lines were down or status on production output vs. planned output against shift target.
3. Visibility:
Having the right production performance and metrics visible to all lines of the shop floor could result in 5-8% uplift in line productivity. Usually, most plants have a chart board listing metrics located near the shift supervisor’s office. Those high-level charts that are sometimes hard to decipher, are at times not current, and the high-level detail is challenging for line personnel to connect to their specific work. So, they are typically ignored.
But, having live metrics automatically calculated and shown live on a monitor screen, or a shift leader making rounds and updating the line performance will have a completely different outcome. The level of engagement tends to improve drastically as root causes for lower performance get immediate attention.
4. Culture:
Never underestimate the role of culture in capturing production issues and actively taking remedial actions to resolve them while the shift is still running. It requires experience (knowledge of lines), delegation of authority, and ownership of the line to identify and remedy the issues that arise during production.
Instill within all employees that the production line is the source of revenue for the company, pays the salaries of the workers, and that a stoppage or delay in the production line is unacceptable. Following up on that notion with right supporting structure to aid production personnel is critical to success.
While the morning meetings may be a bore to workers at companies who have not yet figured it out, if executed correctly, they can make— or break—a manufacturing line’s ability to succeed. Getting it right in terms of metrics and connecting the dots for your workforce can make the difference not only between an engaged or disenfranchised team, but also to the bottom line of the plant.