To get an idea of the labor challenge currently facing the US building industry, consider this. There are more job openings in construction and manufacturing (around 800,000 as of August 2021) than there are total jobs across the mining, quarrying, and oil and gas extraction industries combined.
Attracting and retaining workers has become a critical challenge, one which has undoubtedly been exacerbated by the COVID-19 pandemic. Partly driven by the sudden shift of much of the economy to home working, demand for residential construction quickly outstripped the supply of labor. The virus itself is affecting labor availability. Vaccination rates among construction workers are low and hesitancy remains high.
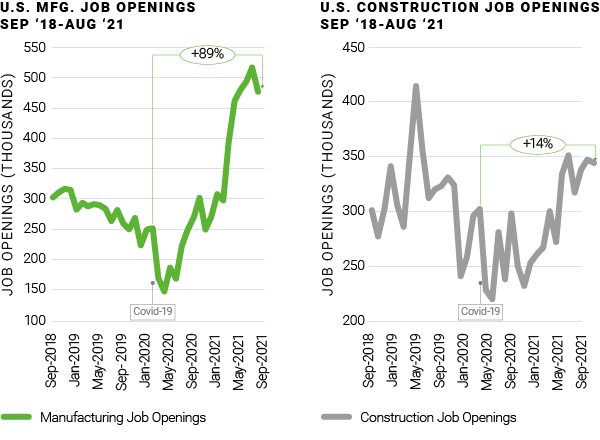
In truth, though, labor availability has been a major concern for many years now, particularly since the recession of 2007-9 which prompted many workers to leave the industry. These challenges are therefore nothing new and cannot be expected to disappear when we fully emerge on the other side of the pandemic.
The impact on wage rates
Employers have resorted to bumping up wages with regularity in an attempt to source enough workers to meet this booming demand. Consequently, labor costs for some construction and manufacturing roles in the US have increased by as much as 9% year-on-year (wage rates in Canada have generally been more stable). All this is happening at the same time as costs for many key building materials, particularly lumber, hit historic highs.
Ultimately, this isn’t sustainable. Rising costs will lead either to compressed margins or, if contractors pass these costs on to their customers, reduced demand further down the line. So what’s the solution?
Automation can ease the strain on labor
Part of the answer must be to address labor supply head-on, through increasing use of automation and robotics.
The ease with which such technologies can be introduced varies significantly throughout the manufacturing and construction value chain, but potential applications exist at every stage, from scanners that can optimise wood-cutting patterns in sawmills, to 3D concrete printing and robotic bricklayers.
Some leading building products manufacturers that have implemented automation solutions at their plants have seen internal rates of return as high as 17% and reduced variable costs equivalent to as many as 50 FTEs.
To reap the rewards of automation, companies must have a coherent strategy for deciding when, where and how to introduce it. As we have discussed in previous blogs, this means developing a structured methodology to evaluate the opportunities and impacts of different types of automation.
Of course, the elephant in the room is that many companies are well aware of what automation could do for them – but they are pushing the required investment and upheaval into the horizon while they focus on the immediate challenges in front of them.
However, while companies may feel they cannot afford the required downtime associated with automation installations right now, they should be getting ready to invest as soon as the market softens. There can be no excuse for looking back in five years’ time at a drastic erosion in profitability, all because of a failure to make intelligent investments in automation now.